Methanization is a rapidly developing technique for the production of biogas. But like many industrial processes, it offers numerous opportunities for optimization: whether to derive maximum efficiency from the methanogenic potential of recycled organic materials, or to reduce its energy and environmental footprint. Thus making “green gas” a more ecological resource.
1/ Biogas production in a methanization unit
Methanization is a biological process that valorizes organic matter (agricultural waste, sludge, household waste) into biogas through anaerobic fermentation. The biogas produced in this way can be used as a renewable energy source, whether for the production of heat, electricity, or as fuel, or can be injected into the network as biomethane. It consists of methane (CH4), but it also contains carbon dioxide (CO₂) and other compounds such as hydrogen sulphide (H₂ S) that must be purified to obtain usable biogas.
However, the methanization process itself consumes energy and the excess biogas is sometimes flared, which generates CO₂ and constitutes an energy loss.
2/ Optimizing performance: the role of artificial intelligence
To improve the efficiency of biogas and reduce the environmental impact of the methanization process, optimizing the methanization processes is essential. The installations are equipped with automatic systems that regulate, for example: organic matter inputs into the digester, biological conditions through temperature management and the agitation of the material, gas purification or its valorization via cogenerators producing heat and electricity.
But these regulations are limited to behaviors essentially in reaction to the occurrence of events such as the temperature threshold being exceeded, the pressure in the gaseous sky, the time spent in the digester or the saturation information of the downstream network. However, while biogas production is directly linked to the organic matter inputs used, its valorization depends on downstream energy demand, in particular by the GRDF network. When the demand for biogas in the network is low, the inertia of the methanization process makes it difficult for methanizers to adapt, and are sometimes forced to flake, and therefore lose part of their production.
Its implementation in the Purecontrol solution provides a detailed predictive view on the behavior of the installation, the production of biogas according to the organic materials used, as well as on the downstream demand (cogeneration) or the availability of the production network (injection). It dynamically anticipates and takes into account events that may affect operations in the calculation of the most effective management strategy. It thus makes it possible to regulate a unit as accurately as possible, to maximize yields while minimizing its ecological footprint: produce as much valuable energy as possible, while consuming as little as possible.
Thus, various optimization strategies are implemented throughout the biogas production and valorization process:
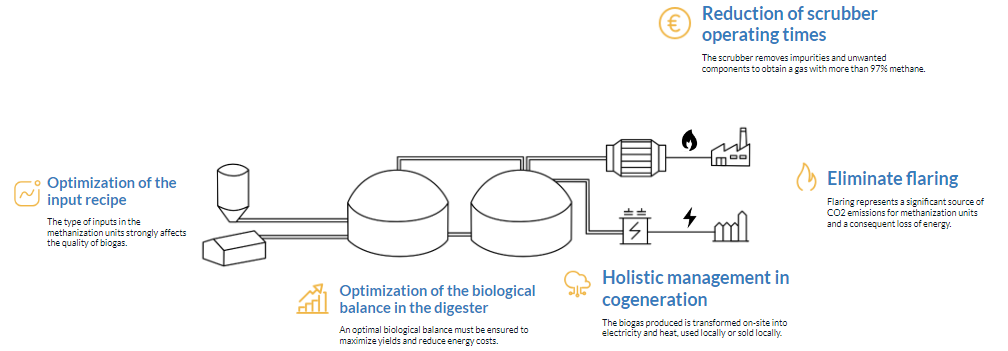
3/ Feedback at Biogaz-IFF with Biogaz IA
Purecontrol intelligent regulation, implemented in the offer Biogaz-IA® by Nevezus, optimizes the entire production process based on data already collected on the units and by managing the periods of gas injection into the networks according to demand.
At Biogaz IFF (Iffendic, 35), this solution has been deployed for almost a year on the most energy-consuming equipment in the installation: the purifier. After a phase of collecting and analyzing the operating data of the purifier, the solution regulates the start of the purifier by predicting the evolution of the level of the gaseous sky (zone where biogas is stored before being extracted and recovered) and taking into account variations in electricity prices.
Concretely, the solution limits the operating time of the purifier as much as possible, it prioritizes its start-up when the energy is the cheapest, all while anticipating periods of saturation of the GRDF network. Thus, the production of green gas is adjusted to demand, and with reduced production costs. Thanks to this control, Biogaz-IFF displays a 14% reduction in the energy cost of its purifier.
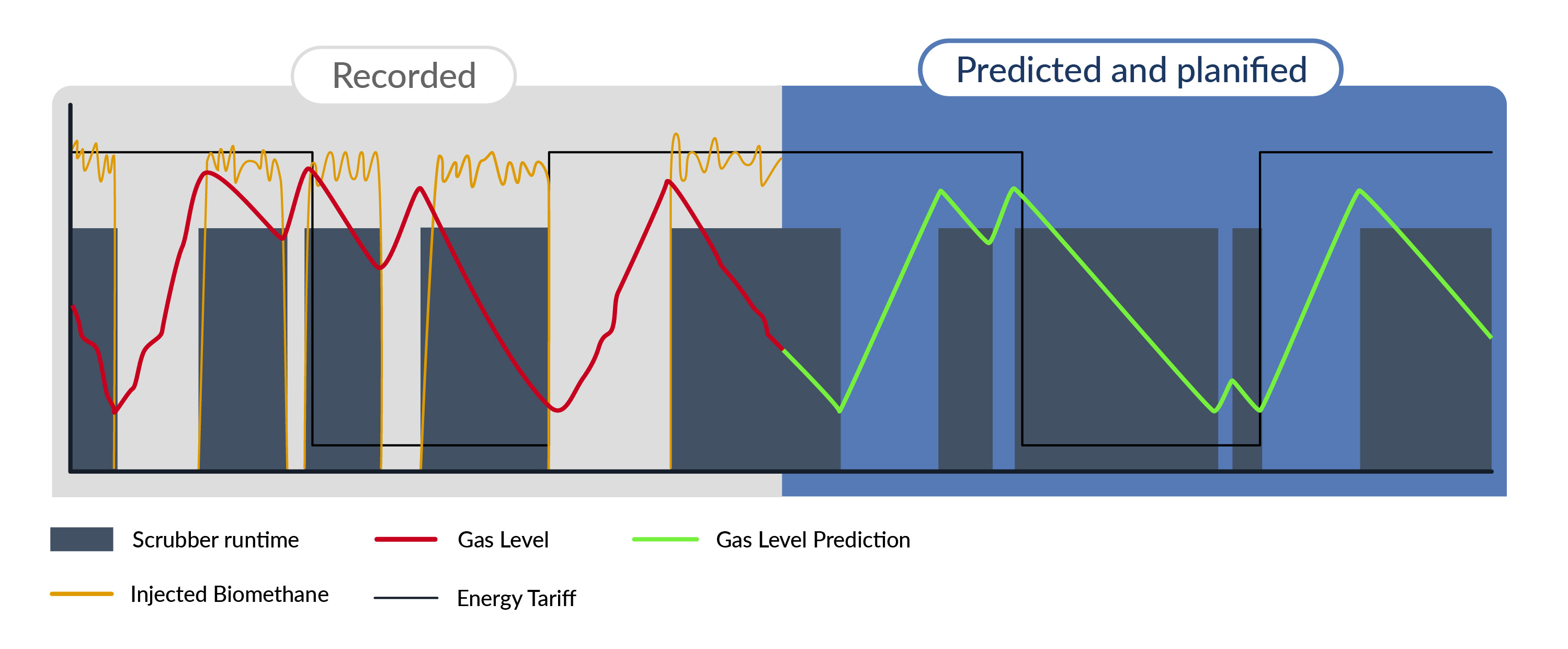
This adaptation to the demand for injection into the network has a second advantage. Since production is adapted to demand, 100% of the biogas produced is recovered, completely eliminates flaring periods, as observed at Biogaz-IFF. No longer producing excess biogas, it is no longer necessary to burn it, thus limiting the release of CO2 into the atmosphere and maximizing the unit's revenues.
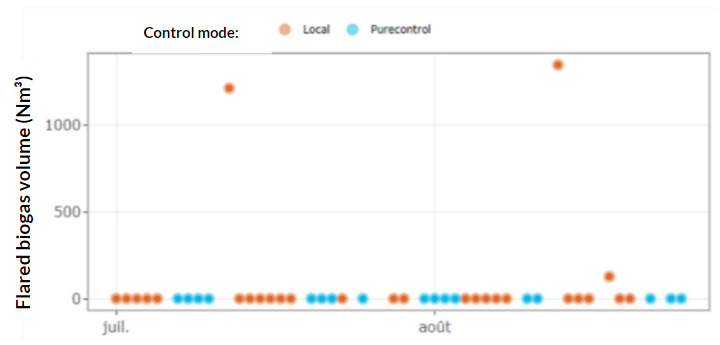
This holistic approach, which integrates multiple internal and external variables in the management of installations (energy demand, energy cost, quality of inputs), makes it possible to continuously optimize the operation of methanizers and to improve the profitability and environmental efficiency of installations. The predictive management of methanization units makes it possible to gain significantly in performance by regulating the installation as accurately as possible. But it also allows operators to change the way they look at their processes and to gain confidence in the management of their installations thanks to predictive process analysis.
In summary, digital technologies, and in particular artificial intelligence, are key levers for making methanization more efficient, making it possible to produce more “green” green gas, both economically and environmentally.
To find out more about Purecontrol's intelligent regulation for methanization, the Biogaz-IA offer, and the feedback on agricultural methanization in Gros-Chêne, (re) -discover this conference held during the Bio360 exhibition held in Nantes in February 2024: Watch the conference
Parcourez le blog
Lorem ipsum dolor sit amet, consectetur adipiscing elit.